With over 85 years of leadership in machine tool design and manufacture, US company Moore Tool – continues to evolve its line of four- and five-axis, CNC-controlled jig grinders. Integrating new enhancements with proven continuous path contouring capabilities, Moore Jig Grinders enable customers to more effectively grind complex two- and three-dimensional surfaces.
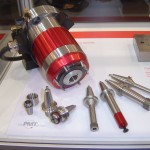
Moore Tool Grinding Spindle Component Parts
Greater accuracy and productivity through powerful new technology
With many recent advances in software and hardware, jig grinding continues to play a critical role in a wide range of small and large scale production applications, where consistency and the highest levels of accuracy and surface finish are required. From mold making to complex part manufacturing, today’s jig grinders deliver the highest degree of accuracy and repeatability required to successfully compete in today’s marketplace. When effectively integrated into other machining operations including EDM and high-speed hard milling – utilizing manual or automated part palletizing system solutions – the enhanced capabilities of today’s jig grinders can create new opportunities with existing customers and open doors to completely new markets.
Taking advantage of these developments, Moore Tool, a leader in building ultra-precision jig grinding equipment, is continuously enhancing the productivity of its jig grinder product line — making it more user friendly and relevant in today’s tool room and higher-volume production environments. While building one of the world’s most accurate grinding machines has been and continues to be the foundation of Moore’s long-term success, a cornerstone of their strategy is to help define customer-specific processes and to help customers fully utilize all the advances in technology in order to create better parts — faster and at a lower cost. Through collaboration with Moore’s experienced Applications Department, customer’s are finding more and more innovative ways to, cost-effectively, utilize jig grinding in their most critical operations.
INTRODUCING MOORE PROGRIND
In today’s competitive markets, manufactures must achieve greater and greater levels of productivity to remain cost effective in today’s global market place.
In response to our customer’s requests, Moore has introduced a number of grinding enhancements, including the Moore ProGrind platform, to support their precision applications – from both small- and large-scale production runs. These new features help empower manufacturers to realize even greater efficiencies, while still achieving sub-micron positioning and surface finishes.
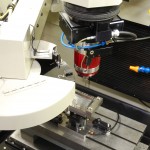
Moore Tool Grinding Spindle
With Moore ProGrind, users reap the time and tool-cost saving benefits that the latest grinding wheel advancements and wet grinding provide. Moore ProGrind features a powerful electric grinding spindle and coolant system for dramatically improved stock removal rates, better surface finishes and longer tool life. Along with the proven grinding spindle and coolant system, companies are grinding with greater confidence, both attended and unattended. These machines are completely CE-compliant, use state-of-the-art sensor technology including remote listening and monitoring capability. Companies are also benefitting from other time saving enhancements such as the 20 position automatic tool changer for unattended operations.
Electric Grinding Spindle
With today’s electric grinding spindle technology, constant torque is maintained throughout the speed range of 10,000 to 60,000 rpm. Superior spindle taper and radial run-out, and greater repeatability tool to tool, helps ensure accuracy when using the 20 tool ATC. The hybrid ceramic ball bearings provide long life and less downtime.
UPDATED SENSOR TECHNOLOGY AND RENISHAW PROBE INTEGRATION
As part of the Moore ProGrind platform, the company has updated its sensor system by integrating the very latest in acoustic emission sensor technology. This technology is fully integrated with Moore Autosize and enables the dynamic measurement of effective wheel diameter and automatic compensation of wheel edge to part edge for precise size finishing of holes and contours. This important technology allows unattended cycles and, in an ideal environment, repeatability to within 3-5 microns.
In addition, the sensor technology is fully integrated with Moore Autogrind an adaptive response system for automatically adjusting feed rates based upon stock encountered in tool path. The system minimizes time spent “grinding air” on work pieces with varied initial stock condition.
Moore has also worked with Renishaw to implement the latest advances in Renishaw’s measuring system. Utilizing their latest technology – the new OMP400 – together with Moore custom macros, measurement uncertainty approaching extremely high levels can be integrated into the grinding cycle.
FANUC’s 31i-a FEATURING THE LATEST IN PC FRONT END CONTROLS
In addition to significant advances in grinding technology, Moore and Fanuc have evolved the Fanuc 31i-a control into the highest performing CNC available for jig grinders today. With improved reliability and ease of use, operators are seeing significant advances in program set-up and work monitoring, with key benefits including:
- 0.0001 mm (0.1 μm) Least Command Increment,
- 0.00001 mm (10 nm) Detect Unit, and
- 16X greater velocity feedback (16 million lines versus 1 million).
- Following error optimized to improve contouring accuracy
In addition to the Fanuc 31i-a, users will benefit from a new PC Front End, featuring:
- 19” Touch Screen Display,
- Ultra-compact, fan-less, fully-sealed, embedded computer,
- Celeron M 1 GHz,
- 1 GB SDRAM,
- 2 GB compact flash for the Operating System and a 2 GB compact flash primarily for customer storage,
- Windows XP Professional embedded,
- 100 base ethernet for system communications with the Fanuc CNC,
- Exterior USB ports, and
- Industrial Sealed Keyboard.
Moore G500 Series
- 500 mm x 300 mm (19.5 in. x 11.8 in.) working surface
- Improved base assembly provides expanded travels and increased stability
- Featuring Moore ProGrind for applications requiring wet grinding
- Fanuc 31i-a control and new, state-of-the-art sensor technology
Moore 1280 Series
- 1280 mm x 835 mm (50.4 in. x 32.9 in.) working surface
- Larger travels for large work or multiple part setups
- Featuring Moore ProGrind for applications requiring wet grinding
- Fanuc 31i-a control and new, state-of-the-art sensor technology
IN SUMMARY
As a manufacturer, staying ahead of the competition with the latest advances in equipment, software and processes is essential. In keeping up with these challenges, machine tool makers must continuously innovate to provide their manufacturing customers more accurate and more productive equipment. Today, Moore Tool jig grinders come standard with features that make the machine extremely productive and easy to operate. With these advances, the modern jig grinder continues to play an essential role in the most complex operations requiring superior accuracy, productivity and surface finish.
For further information please contact Norman Loughton, UK Sales Agent:
NL Machine Tool Consulting
T: +44 (0)1908 675434
M: +44 (0)7944 401177